行业资讯
济南沥青生产厂家:沥青生产的精密之旅
来源:http://www.ycgjglcl.com/ 日期:2025-05-27
在道路建设领域,沥青作为路面铺装的核心材料,其生产过程犹如一场精密的化学交响乐。从深埋地下的原油到黝黑发亮的道路建材,每一滴沥青都经历着复杂的物理化学转变。本文将深度解析沥青生产的全流程工艺,揭示这种常见建材背后的科技奥秘。
In the field of road construction, asphalt, as the core material for pavement, is produced like a precise chemical symphony. From deeply buried crude oil to dark and shiny road building materials, every drop of asphalt undergoes complex physical and chemical transformations. This article will deeply analyze the entire process of asphalt production and reveal the technological secrets behind this common building material.
一、原料预处理:基础材料的精制艺术
1、 Raw material pretreatment: the refined art of basic materials
沥青生产的原料体系包含三重保障:以减压渣油为主的基质原料,占总量70%-85%;作为改性剂的催化油浆,提供关键的胶体结构;以及专用的添加剂包,包含稳定剂、抗氧化剂等组分。原料进入生产系统前,需经三级过滤净化,首先通过80目振动筛去除机械杂质,再经电脱水器脱除95%以上的游离水,最后进入真空干燥塔,在150℃、-0.09MPa条件下将含水量降至0.1%以下。
The raw material system for asphalt production includes three guarantees: matrix raw materials mainly composed of vacuum residue, accounting for 70% -85% of the total; As a modifier, catalytic slurry provides key colloidal structures; And a dedicated additive package, including stabilizers, antioxidants, and other components. Before entering the production system, the raw materials need to undergo three-stage filtration and purification. Firstly, mechanical impurities are removed through an 80 mesh vibrating screen. Then, more than 95% of free water is removed through an electric dehydrator. Finally, it enters a vacuum drying tower and the water content is reduced to below 0.1% at 150 ℃ and -0.09MPa.
预处理环节的核心设备是减压蒸馏塔,其塔盘间距经过流体力学优化,确保渣油在塔内形成稳定的逆流接触。通过精确控制塔顶压力(2-5kPa)和塔底温度(360-380℃),实现渣油中轻质组分与重质组分的精准分离。某炼化企业实测数据显示,该工艺可使渣油软化点波动范围控制在±1.5℃以内。
The core equipment of the preprocessing stage is the vacuum distillation tower, whose tray spacing is optimized by fluid mechanics to ensure stable countercurrent contact of residual oil inside the tower. By precisely controlling the top pressure (2-5kPa) and bottom temperature (360-380 ℃), precise separation of light and heavy components in residual oil can be achieved. The actual test data of a certain refining enterprise shows that this process can control the fluctuation range of residual oil softening point within ± 1.5 ℃.
二、氧化工艺:核心性能的锻造工坊
2、 Oxidation process: forging workshop for core performance
氧化反应是沥青品质成型的关键阶段。连续式氧化生产系统由氧化塔、换热网络、尾气处理单元构成。原料在氧化塔内经历三个温度区间:预热段(200-230℃)、反应段(250-280℃)、熟化段(230-250℃)。在反应段,压缩空气以0.8-1.2m?/kg的配比注入,引发深度氧化缩合反应。
Oxidation reaction is a critical stage in the formation of asphalt quality. The continuous oxidation production system consists of an oxidation tower, a heat exchange network, and a tail gas treatment unit. The raw materials undergo three temperature ranges in the oxidation tower: preheating section (200-230 ℃), reaction section (250-280 ℃), and maturation section (230-250 ℃). In the reaction section, compressed air is injected at a ratio of 0.8-1.2m/kg to initiate a deep oxidation condensation reaction.
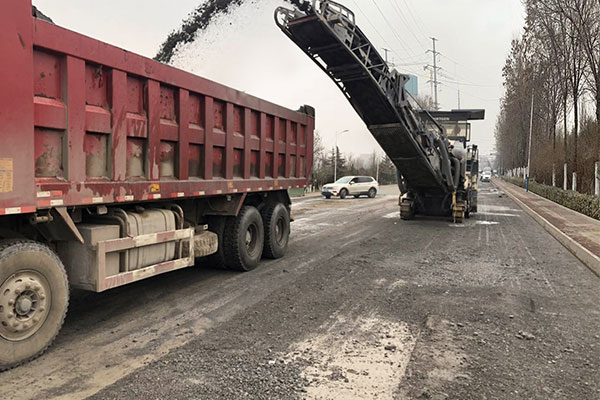
该过程的核心控制参数是反应温度和空气流量。采用模糊PID控制算法,建立温度-粘度-针入度的三维关联模型,实现工艺参数的动态优化。某沥青生产企业的中试数据显示,当反应温度波动±2℃时,成品沥青的60℃动力粘度变化率可达8%,凸显了精准控制的重要性。
The core control parameters of this process are reaction temperature and air flow rate. Adopting the fuzzy PID control algorithm, a three-dimensional correlation model of temperature viscosity penetration is established to achieve dynamic optimization of process parameters. The pilot data of a certain asphalt production enterprise shows that when the reaction temperature fluctuates by ± 2 ℃, the 60 ℃ dynamic viscosity change rate of the finished asphalt can reach 8%, highlighting the importance of precise control.
为提升氧化效率,现代生产线引入微纳米气泡技术。通过特殊设计的文丘里管,将空气分散为直径50-100μm的微气泡,使气液接触面积提升3倍,氧化反应速率提高25%。该技术使氧化时间缩短至传统工艺的60%,同时降低能耗18%。
To improve oxidation efficiency, modern production lines introduce micro nano bubble technology. By using a specially designed Venturi tube, the air is dispersed into microbubbles with a diameter of 50-100 μ m, increasing the gas-liquid contact area by three times and increasing the oxidation reaction rate by 25%. This technology shortens the oxidation time to 60% of traditional processes, while reducing energy consumption by 18%.
三、改性工艺:性能升级的创新引擎
3、 Modified technology: an innovative engine for performance upgrade
针对不同应用场景,沥青需进行深度改性处理。SBS改性工艺采用高速剪切机,在180-190℃条件下将苯乙烯-丁二烯-苯乙烯嵌段共聚物(SBS)与基质沥青混合。剪切头转速达5000rpm,产生的高剪切力使SBS颗粒细化至5μm以下,形成稳定的海岛结构。某高速公路项目应用表明,该工艺使沥青高温稳定性提升3倍,低温抗裂性改善40%。
Asphalt needs to be deeply modified for different application scenarios. The SBS modification process uses a high-speed shearing machine to mix styrene butadiene styrene block copolymer (SBS) with matrix asphalt at 180-190 ℃. The shear head rotates at 5000rpm, generating high shear force that refines SBS particles to below 5 μ m, forming a stable island structure. The application of a certain highway project shows that this process increases the high-temperature stability of asphalt by three times and improves the low-temperature crack resistance by 40%.
对于特种需求,采用复合改性技术。将纳米蒙脱土、石墨烯等功能材料与SBS协同作用,通过溶液共混法实现纳米级分散。透射电镜观察显示,复合改性剂在沥青中形成三维网状结构,使沥青的抗车辙能力提升50%,疲劳寿命延长3倍。
For special requirements, composite modification technology is adopted. By synergistically combining functional materials such as nano montmorillonite and graphene with SBS, nanoscale dispersion can be achieved through solution blending. Transmission electron microscopy observation shows that the composite modifier forms a three-dimensional network structure in asphalt, which increases the anti rutting ability of asphalt by 50% and prolongs the fatigue life by three times.
四、成品精制:品质保障的最后防线
4、 Finished product refinement: the last line of defense for quality assurance
成品沥青需经三级精制:首先通过高速离心机脱除机械杂质,再经薄膜蒸发器脱除轻组分,最后进入成品罐进行陈化。陈化过程采用智能温控系统,在150-160℃条件下保持72小时,使沥青组分充分缔合,消除内应力。
The finished asphalt needs to be refined in three stages: first, mechanical impurities are removed by a high-speed centrifuge, then light components are removed by a thin film evaporator, and finally it enters the finished product tank for aging. The aging process adopts an intelligent temperature control system, which maintains a temperature of 150-160 ℃ for 72 hours to fully combine the asphalt components and eliminate internal stress.
质量控制体系包含23项检测指标,涵盖物理性能(针入度、软化点、延度)、化学组成(饱和分、芳香分、胶质、沥青质)、路用性能(动稳定度、弯曲应变)三大维度。采用近红外光谱技术建立快速检测模型,可在2分钟内完成主要指标的筛查,检测结果与传统方法偏差小于3%。
The quality control system includes 23 testing indicators, covering three dimensions: physical properties (penetration, softening point, ductility), chemical composition (saturation fraction, aromatic fraction, resin, asphalt), and road performance (dynamic stability, bending strain). Using near-infrared spectroscopy technology to establish a rapid detection model, the screening of main indicators can be completed within 2 minutes, and the deviation between the detection results and traditional methods is less than 3%.
沥青生产工艺的进化,是材料科学与过程工程深度融合的典范。从原料精选到深度改性,从氧化缩合到智能精制,每个环节都凝聚着工程技术的智慧。这种精密制造不仅赋予沥青优异的路用性能,更推动着道路建设向绿色化、智能化方向发展。当一辆辆汽车平稳驶过黑色路面时,背后正是这场跨越物理化学界限的品质锻造之旅。
The evolution of asphalt production technology is a model of deep integration between materials science and process engineering. From raw material selection to deep modification, from oxidation and condensation to intelligent refining, every step embodies the wisdom of engineering technology. This precision manufacturing not only endows asphalt with excellent road performance, but also promotes the development of road construction towards green and intelligent direction. As cars smoothly cross the black road surface, behind them lies a journey of forging quality that transcends physical and chemical boundaries.
This article is a friendly contribution from Jinan Water Stable Mixing Plant For more information, please click: http://www.ycgjglcl.com Sincere attitude To provide you with comprehensive services We will gradually contribute more relevant knowledge to everyone Coming soon.